Supply Chain solution from A to Z - Best Practice
20 May 2020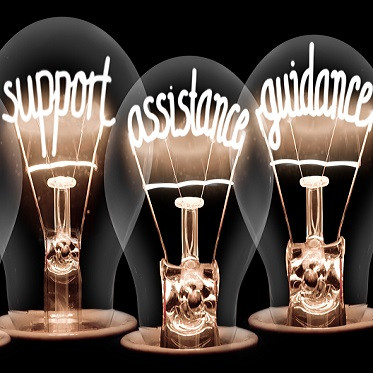
In today’s rapidly changing environment organizations are challenged when it comes to keeping their Supply Chain going. KLG plays a crucial role in resolving the challenges our customers face through support in identifying the challenge at hand, determining the best possible solution and installing of that same rigid solution. We invest in long-term partnerships.
A good example would be the company Mayfran, based in Landgraaf (NL), a global leader in providing solutions for scrap and coolant management and material handling in metalworking, recycling and solid waste processing.
Mayfran approached KLG regarding the relatively high percentage of damages identified during movement of the goods, long lead times and the relatively high storage costs they were facing. Vital aspects as good communication, reporting and visibility where lacking at the time.
As soon as KLG had gathered all necessary shipment data, clearly understood customer’ processes and requirements, we started with the design and build up of a tailor-made solution. At KLG we have the expertise for the various processes within the total Supply Chain all embedded within the organization. The team includes data analysts from the Tender Team, Cross dock Manager, Warehouse Manager, Operations Manager, IT analyst, Marketing, Legal & Quality Manager and an Account Manager.
This team processed the information within their own field of expertise. Through interpretation of their recommendations a total concept solution was created which in turn evolved to a concise plan of action.
In agreement and with commitment from Mayfran's management team, the actions were presented to the operational team. Commitment to follow through on the actions and implement the new way of working was instant. Both parties became partners and can now reflect on a successful implementation.
The concept offered by KLG Europe:
In the original situation, all Mayfran products were transported daily with two shuttles to a storage location and from there the goods were sent to the end recipients of Mayfran. This way of transport, with multiple transshipments, resulted in a large number of damaged shipments. After an analysis of the shipment structure KLG concluded that it was better to load all shipments larger than 2 loading meters directly in Landgraaf and to deliver on wheels to their customers. By also using one combined shuttle daily for storage and groupage shipments handling for Mayfran was reduced and storage costs reduced. The risk for damages was also lowered. Ultimately, within one year, KLG was able to reduce the number of controllable claims by 97% compared to the previous situation.
The above implementation also resulted in shorter lead times to the end customers. Mayfran adapted the internal processes in terms of order administration and production, when an order was ready, it could be delivered faster. The lead times for road transport were reduced by an average of two days. An additional advantage is that the customer’s cash flow improved because clients were now paying sooner as a result of the earlier deliveries. Furthermore, the new setup reduced the number of urgent shipments by roughly 95%, which has resulted in enormous cost savings. The reduction in urgent shipments relieved the pressure on the overall processes within Mayfran and thus resulted in accurate costing towards customers.
KLG’s IT department also implemented a monthly reporting tool through combining data the WMS and TMS systems. The reports show the analysis of customer data on a monthly basis. All actions are defined and monitored accordingly. The reporting is applicable to both road transport and warehousing. KLG built a calculation tool, linked to our booking system which enables Mayfran to instantly calculate the costs per shipment. As a result, they have less administrative work in their logistics department, which means that the indirect costs decreased. The new concept has resulted in higher efficiency and better transparency, which has ultimately resulted in reduced personnel costs.
We have also optimized communication and transparency towards each other by working with one contact person, specifically for Mayfran, within KLG Europe. In addition, there is a track & trace system in which they can follow their shipments real-time. We also have quarterly business reviews where improvement projects from both Mayfran and KLG perspective are discussed. Through direct communication decisions can be made quickly on both sides if desired, which ultimately benefits the end result.
The mutual approach has not only resulted in KLG achieving cost savings directly and indirectly for Mayfran, it is also a textbook example of collaboration between two organizations. Together we stand stronger.
Thanks to mutual trust throughout both Mayfran and KLG Europe organizations we have been able to achieve a common goal with great success!
Wondering if your Supply Chain can also be improved, what KLG Europe can do for you and how we can become a partner? Contact us!
T+ 31 (0) 77 324 50 00 – info@klgeurope.com